Visualizing Jobs in a Carbon Removal Economy
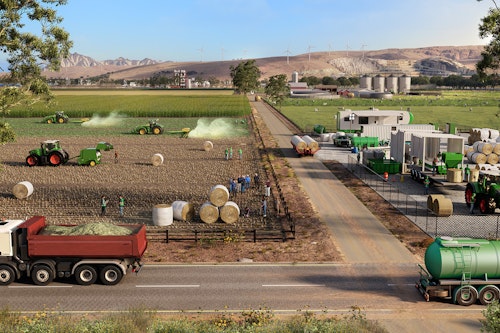
Carbon dioxide removal (CDR) technologies have the potential to create hundreds of thousands of good-quality, well-paying jobs for everyday Americans while also removing significant carbon emissions from the atmosphere. However, the global CDR industry is still nascent, with many of these technologies currently operating at the lab or pilot scale. Realizing the economic and climate benefits of CDR will require rapid buildout of these technologies across a range of geographies. And the US is primed to do just that.
While federal policies—such as the Bipartisan Infrastructure Law and Inflation Reduction Act—have boosted US CDR leadership, America’s legacy industries also give us an advantage in these emerging technologies. Many of the jobs needed to develop and deploy CDR will require skills that are directly transferrable from well-established sectors such as oil and gas or agriculture. These businesses, their workforce, and the communities they operate in will play a major role in bridging the gap between early-stage research and development and large-scale deployment of novel CDR technologies in the US.
Since we’re talking about novel technologies and complex systems, we thought it was better to show, not just tell. Third Way collaborated with Gensler, a world-renowned architecture and design firm, to create a series of renderings showcasing how America’s workers and infrastructure can plug into the growing opportunities for CDR. We also conducted qualitative interviews with a broad range of CDR technology developers to gain a better understanding of the kinds of jobs, industries, and community engagement opportunities that developers envision during construction, operations, and maintenance of these projects.
How to Navigate This Memo
For this project, we produced two rendering storyboards—one depicting marine CDR (mCDR) technologies near a coastal city and the other depicting terrestrial CDR technologies near a rural township. Each storyboard begins with a birds-eye view of a CDR tech ‘ecosystem’ containing multiple clusters of CDR-related projects followed by four, zoomed-in scenes displaying the details of these clusters. Each zoomed-in scene is accompanied by an icon overlay identifying the jobs illustrated in these zoomed-in scenes.
Jobs are organized based on where they are in the CDR value chain, in order to more easily compare them to similar jobs in other parts of today’s economy. These value chain segments include: 1) raw materials, 2) project development, 3) engineering, procurement, construction (EPC), 4) operations and maintenance, and 5) transport and storage. We also included a separate category for indirect jobs, i.e., jobs not directly involved in developing, deploying, and operating commercial-scale CDR projects but that can still benefit from these projects.
How to Use These Renderings
These renderings can be helpful for engaging with potential project host communities, discussing project labor agreements with labor unions, educating local institutions about prospective economic opportunities, etc. We encourage readers to share these images and use them to educate stakeholders on CDR, garner interest by showing how CDR can benefit Americans, and ultimately build a larger and more diverse base of supporters for CDR development and deployment in the US.
You can click on each rendering and icon overlay to view the image in a larger format. You can also click here to view, download, and share all the images in this memo. Please credit all images to Third Way.
Marine Carbon Removal
1. Marine Carbon Removal—Full Ecosystem

Scene Description
This first scene provides an overview of the different ways in which marine CDR (mCDR) technologies can be integrated into an industrial-port zone just outside of a coastal city. Legacy port and coastal infrastructure have been combined with commercial-scale mCDR projects to demonstrate how these sectors can co-exist to form an mCDR ‘ecosystem.’ At the center of the complex, a desalination plant has been retrofitted with two different mCDR projects. Clean hydrogen transport and storage facilities, along with liquefied hydrogen carriers and long-haul fuel cell trucks, can be seen scattered throughout the industrial port. On the outskirts of the port, a decommissioned offshore oil rig has been revitalized as an offshore mCDR plant. Further up the coast, small-scale mCDR methods are being deployed in aquaculture pens and along the beach of a marine science center complex. The subsequent scenarios take a closer look at how these mCDR projects fit into these different settings and the types of jobs created through the deployment of these projects.
2. Marine Carbon Removal at a Desalination Plant
Scene Description
In this scene, two commercial-scale, modular direct ocean capture (DOC) projects have been integrated into a coastal desalination plant. Desalination plants are ideal sites for DOC projects as they provide the intake and processing infrastructure needed to move large volumes of seawater to achieve commercial-scale DOC operations. In exchange, DOC projects turn a would-be waste product into a climate mitigation tool and a supplementary revenue stream for desalination plants. Here, the waste brine produced during the desalination process is being re-purposed for two methods of DOC, both of which use low-carbon electricity to separate the waste brine into an acid and a base stream.
The project with yellow pipelines moves the waste brine through multiple sets of electrodialysis systems housed in hangars. The separated base stream is then piped into a small pond before cascading into the ocean, where the dissolved alkaline minerals in the base stream bond with dissolved CO2 and transform it into a stable, dissolved carbon compound for permanent sequestration. This base stream can also reduce local ocean acidification and/or be used in aquaculture (see Scene 5).
The project with blue pipelines includes a set of DOC modules under construction and another set of DOC modules operating behind it. Here, we see how each unit of the DOC project can function independently but still work together to achieve commercial-scale CDR. Behind the construction site, the operational DOC modules move the waste brine through multiple sets of electrolyzers. The separated base stream then goes through air contactors housed in cooling towers where dissolved alkaline minerals in the base stream bond with CO2 from the ambient air. The once ambient CO2 gas is now permanently trapped in the base stream as a dissolved carbon compound. Afterwards, the base stream containing the dissolved carbon compound is mixed with a neutralized acid stream and poured into a small pool before cascading into the ocean for permanent carbon sequestration. Not all the CO2 captured by the base stream turns into dissolved carbon. Some of the CO2 is also turned into white calcium carbonate minerals, which are being transported in yellow dump trucks to be used for local beach restoration (see Scene 5).
Both DOC projects also produce carbon-negative hydrogen alongside carbon removals. This hydrogen can be used to power their DOC processes or for other purposes. Tanker trucks can be seen transporting hydrogen produced via DOC to the nearby industrial-port zone (see Scene 4).

Job Descriptions
- Carbon Monitoring Inspectors: Collect water samples and analyze data output from electrodialysis equipment for monitoring, reporting, and verification (MRV). Trained professionals, such as marine and environmental scientists, incorporate the data collected into highly sophisticated models to ensure that the base streams produced by the DOC facilities safely and effectively sequester carbon.
- Construction Workers: Build the infrastructure of the DOC facilities. Includes welders, pipefitters, plumbers, electricians, heavy equipment operators, etc.
- Engineers: Work alongside construction to install the more technical components of the DOC facilities, e.g., the electrodialysis kit, and ensure the integrity of the systems being built. Includes mechanical, industrial, chemical, civil, and electrical engineers.
- Mechanical, Electrical, and Plumbing (MEP) Maintenance: Maintain the various heating, ventilation, and air conditioning (HVAC), electrical, and plumbing systems integrated into all the DOC facilities.
- Computer-Controlled Tool Operators: Operate the computer systems controlling the technical machinery of the DOC facilities, i.e., the electrodialysis kit, air contactors, water transportation systems, etc.
- Process Engineers: Perform engineering and operation activities to ensure the various biochemical steps involved in the DOC processes are working optimally.
- Operations Management and Supervision: Oversee the general operations of all the DOC facilities to ensure safety and efficiency.
- Vehicle Operators: Operate a variety of vehicles, such as dump trucks carrying crushed calcium carbonate and tanker trucks carrying hydrogen produced via DOC.
- Desalination Plant Operators: Operate and maintain intake, pre-treatment, desalination, post-treatment, and distribution processes at the desalination plant.
- Health, Safety, and Environment (HSE) Officers: Minimize hazards, prevent accidents and injuries, and promote environmentally safe and sustainable practices to protect the health and safety of DOC facility workers.
3. Marine Carbon Removal on an Offshore Rig
Scene Description
Offshore, we see a decommissioned oil and gas rig that has been retrofitted with a commercial-scale, modular direct ocean capture (DOC) facility. Such a retrofit makes sense for several reasons. It cuts capital costs for DOC project deployment by repurposing existing platform, pipeline, and cargo transport infrastructure. It also provides a cost-efficient means of extending the life of an aging rig and prolonging the employment of existing offshore rig workers. Many of the disciplines traditionally required for offshore oil and gas extraction, such as engineering, drilling operations, wellhead and pipeline maintenance, etc., would also be applicable and transferable to offshore CO2 injection captured via DOC.
In this scene, seawater is being pumped onto the platform via pipelines where it undergoes pre-treatment to remove minerals and soften the seawater. The processed seawater then goes through electrodialysis systems which use electricity to separate a small portion of the collected seawater into an acid and a base stream.
The electrodialysis process uses zero-emissions electricity provided by floating solar platforms. The acid stream is used to extract CO2 from the larger portion of seawater and is eventually neutralized with the base stream. The CO2 stream is compressed and injected deep beneath the seafloor via a pipeline connected to a depleted oil and gas well. The neutralized seawater is then pumped back into the ocean with a restored capacity to absorb CO2 from the air. A hydrogen-powered airplane can be seen taking off in the distance.

Job Descriptions
- Carbon Monitoring Inspectors: Collect water samples and analyze data output from both the electrodialysis and CO2 injection equipment for monitoring, reporting, and verification (MRV). Trained professionals, such as marine and environmental scientists, incorporate the data collected into highly sophisticated models to ensure that the CO2 is being safely and effectively sequestered. They also ensure that the neutralized seawater being returned to the ocean is not negatively impacting the marine environment.
- Mechanical, Electrical, and Plumbing (MEP) Maintenance: Maintain the various heating, ventilation, and air conditioning (HVAC), electrical, and plumbing systems integrated into all the DOC facilities on the offshore rig.
- Computer-Controlled Tool Operators: Operate the computer systems controlling the technical machinery of the DOC facility, i.e., the seawater pre-treatment kit, electrodialysis kit, water transportation systems, CO2 gas extractor, CO2 injection systems, etc.
- Process Engineers: Perform engineering and operation activities to ensure the various biochemical steps involved in the DOC processes as well as the processing steps in CO2 capture and sequestration are working optimally.
- Roustabouts and Roughnecks: Roustabouts and roughnecks execute the manual tasks on a rig. While their specific duties differ slightly, both are involved in moving, maintaining, and repairing equipment around the rig floor so that others can do their jobs safely and efficiently. They also assist other workers with a wide range of operations and maintenance tasks on the rig floor.
- Wellhead Operators: Operate and maintain the engines, pumps, hoses, etc. involved in piping captured CO2 beneath the seafloor for permanent carbon sequestration.
- Service Unit Operators: Maintain CO2 flow through pipelines and perform safety and maintenance inspections on pipeline equipment.
- Operations Management and Supervision: Oversee the general operations of the offshore DOC facility and other tasks on the platform to ensure safety and efficiency.
- Supply Vessel Operators: Operate maritime vessels transporting personnel and cargo to and from the offshore rig.
- Helicopter Pilots: Operate helicopters transporting personnel and cargo to and from the offshore rig.
- Crane Operators: Operate cranes to load and unload cargo for the offshore rig.
- Health, Safety, and Environment (HSE) Officers: Minimize hazards, prevent accidents and injuries, and promote environmentally safe and sustainable practices to protect the health and safety of offshore rig workers.
4. Marine Carbon Removal at a Hydrogen Industrial Port
Scene Description
Back onshore, we see how hydrogen transport, storage, and offtake infrastructure have been integrated into an industrial-port zone. Hydrogen provides a viable pathway to cut pollution from sectors such as maritime shipping, port operations, long-haul trucking, and aviation. Sourcing hydrogen from direct ocean capture (DOC) projects not only boosts the economic case for marine CDR (mCDR), but also reduces the emissions intensity of the hydrogen produced and used.
Here, hydrogen is being moved around in various forms, including liquefied hydrogen carriers (large vessels/ships) or potentially in the form of ammonia on trucks. Notably, hydrogen by itself can be tricky to transport and store, and it is often combined with other compounds to make various fuels, including methanol or ammonia. In this setting, the hydrogen being transported or stored has been sourced from nearby DOC projects (see Scene 2), which produce low-carbon or even carbon-negative hydrogen alongside carbon removals.
For example, we illustrate an ammonia-powered ship with spherical tanks storing liquefied hydrogen that has just been docked. Spherical tanks are ideal for securely storing hydrogen due to their ability to withstand high-pressure and maintain proper storage conditions. Liquefied hydrogen from the tanks aboard the ship is being piped into storage containers onshore and can be further used as feedstock to produce ammonia, methanol and other synthetic fuels.
At the front of the scene, additional hydrogen storage tanks are being constructed to increase the port’s storage capacity. Next to the construction site, a tanker truck carrying hydrogen produced via DOC can be seen. Further back, a fueling station provides hydrogen to power long-haul fuel cell trucks that are transporting cargo and potentially methanol or ammonia from the port to far away locations.

Job Descriptions
- Construction Workers: Build the liquefied hydrogen storage tanks and pipeline infrastructure. Includes welders, pipefitters, plumbers, electricians, crane operators, etc.
- Engineers: Work alongside construction to install the more technical components involved in safely storing and transporting liquefied hydrogen. Includes mechanical, industrial, chemical, civil, and electrical engineers.
- Mechanical, Electrical, and Plumbing (MEP) Maintenance: Maintain the various heating, ventilation, and air conditioning (HVAC), electrical, and plumbing systems integrated into all the hydrogen storage kit, fueling stations, port facilities, and commercial ships.
- Computer-Controlled Tool Operators: Operate the computer systems controlling the machinery involved in maintaining temperature, pressure, etc. of the liquefied hydrogen storage and transport infrastructure.
- Process Engineers: Perform engineering and operation activities to ensure that the hydrogen is being transported and stored safely and efficiently.
- Hydrogen Fuel Station Operators: Operate and maintain the pumps used to refuel fuel cell-powered long-haul trucks.
- Hydrogen Vehicle Operators: Operate long-haul fuel cell trucks carrying various fuels made from hydrogen produced via DOC to far away locations.
- Port Equipment Operators: Operate the various heavy equipment involved in handling port cargo, such as gantry cranes used to move shipping containers.
- Longshore Workers: Execute the day-to-day tasks involved in unloading and loading cargo from ships, as well as any other duties associated with port operations.
- Health, Safety, and Environment (HSE) Officers: Minimize hazards, prevent accidents and injuries, and promote environmentally safe and sustainable practices to protect the health and safety of construction site workers and longshore workers.
5. Marine Carbon Removal at a Marine Science Center
Scene Description
Away from the hustle and bustle of industrial activities, smaller-scale marine CDR (mCDR) methods have been integrated into a coastal marine science center. This scene underscores the value of partnering with local institutions to educate and engage with communities on mCDR. Engaging communities early and often on innovative technologies, such as mCDR, can help build support and ensure the successful buildout of these projects.
Slightly offshore, we see aquaculture pens housing various fish, kelp, and shellfish. Traversing on boats are aquaculture farmers dumping an alkaline solution produced via direct ocean capture (DOC) (see Scene 2) into pens to sequester dissolved CO2, reduce local water acidity, and boost marine life growth. Along the shore, beach maintenance workers are spreading two types of crushed up minerals. Dark green olivine minerals are being spread along the beach to remove and sequester CO2 from seawater washing upon the shore via coastal carbon capture. White calcium carbonate minerals are being spread along the beach to replace sand that has washed away over time.
Back at the marine science center, novel mCDR and monitoring, reporting, and verification (MRV) methodologies are being tested along with other marine science experiments. Educators work alongside the marine scientists to teach visiting students and families about lab studies being conducted at the center. Out on the observation pier, students and families get to take their learnings from the marine science center labs and witness the real-world applications of mCDR. On the beach, students and families are learning about MRV for coastal carbon capture.

Job Descriptions
- Carbon Monitoring Inspectors: Collect water samples and analyze data output from buoys for MRV. Trained professionals, such as marine and environmental scientists, incorporate the data collected into highly sophisticated models to ensure CO2 is being safely and effectively sequestered by the olivine minerals on the beach and the alkaline solution in the aquaculture pens.
- Aquaculture Farmers: Care for the various marine life in the aquaculture pens, which includes handling the alkaline solution produced via DOC in a safe and effective manner.
- Beach Maintenance Workers: Ensure that the olivine and calcium carbonate minerals are evenly spread across the beach.
- Heavy Equipment Operators: Operate various heavy machinery, such as loaders and beach diggers, handling the olivine and calcium carbonate minerals on the beach.
- Vehicle Operators: Operate a variety of vehicles, such as dump trucks transporting the olivine and calcium carbonate minerals to the beach.
- Marine Scientists: Conduct various marine science studies in both indoor and outdoor lab spaces. Some of these studies focus on novel mCDR and MRV methodologies.
- Educators: Engage with and educate students and families visiting the marine science center on mCDR and its impact on climate and marine ecosystems.
Terrestrial Carbon Removal
1. Terrestrial Carbon Removal—Full Ecosystem
Scene Description
This first scene provides an overview of the various ways terrestrial CDR technologies can be integrated near an inland township. Traditional rural landscapes have been combined with commercial-scale terrestrial CDR projects to showcase how these technologies can co-exist to form a terrestrial CDR ‘ecosystem.’ At the front of our scene, an agricultural plot has become a hub of terrestrial CDR, where crop harvests and carbon removals take place side-by-side. In the distance, a quarry acts as both a carbon removal site and a feedstock source for other terrestrial CDR projects. Near the center of our ecosystem, several abandoned oil and gas fields have been transformed into injections sites for various forms of carbon. The following scenarios take a closer look at how these terrestrial CDR projects fit into these different settings and the types of jobs created through the deployment of these technologies.
2. Terrestrial Carbon Removal at a Quarry
Scene Description
Past the river, we see how a quarry can be a source of carbon-removing minerals and a site where terrestrial CDR takes place. This scene showcases how one industry’s trash can be another one’s treasure. Materials that would otherwise be disposed of can be repurposed for enhanced rock weathering (ERW) in which minerals capable of sequestering carbon are mixed with water to remove CO2 from the ambient air. ERW can be minimally invasive to the quarry, cost-effective for the CDR project developer, and utilizes existing quarry jobs and skillsets. Using quarry waste for ERW can also create an additional revenue stream for mining companies.
During quarrying operations, fine rock dust is often washed off rocks before delivery and stockpiled into either dry waste piles or mixed with water and stored in tailings dams. However, this rock dust should hardly be considered waste. Waste piles and tailings dams can contain valuable minerals used for ERW.
At this quarry, charcoal black basalt and earthy green olivine dusts are being organized into two large piles. Olivine and basalt are ideal for sequestering carbon via ERW due to their weathering and chemical characteristics. Dump trucks can be seen carrying basalt and olivine dust to be used for ERW elsewhere (see Scene 3). These minerals are also being transported on barges along local waterways to projects in other counties (see Scene 1). Off to the side, autonomous rovers traverse across the surface of the tailings dam and conduct ERW by mixing the mine tailings with water.

Job Descriptions
- Quarry Heavy Equipment Operators: Operate the various heavy machinery involved in collecting quarry rocks, such as excavators, loaders, etc.
- Mining Engineers: Design mines and oversee the efficient extraction and processing of quarried rocks.
- Geologists: Conduct geologic surveying and pit ore control to guide mining operations. Includes mineralogists who analyze the composition of various quarried rocks to assess their fit for ERW use.
- Computer-Controlled Tool Operators: Operate the computer systems controlling the quarry processing machinery, i.e., the crushers, screeners, conveyors, etc.
- Operations Management and Supervision: Oversee the general operations of the quarry to ensure safety and efficiency.
- Carbon Monitoring Inspectors: Collect samples of mine tailings and analyze data output from autonomous rovers for monitoring, reporting, and verification (MRV). Trained professionals, such as mineralogists, incorporate the data collected into highly sophisticated models to ensure that the CO2 is effectively being mineralized and sequestered in the tailings dam.
- Field Technicians: Provide on-site technical support and maintenance for the autonomous rovers.
- Vehicle Operators: Operate a variety of vehicles, such as haul and dump trucks transporting olivine and basalt dust from the quarry to other terrestrial CDR projects.
- Health, Safety, and Environment (HSE) Officers: Minimize hazards, prevent accidents and injuries, and promote environmentally safe and sustainable practices to protect the health and safety of quarry workers.
3. Terrestrial Carbon Removal and Agriculture
Scene Description
A few miles away, we see how terrestrial CDR has been integrated into a crop farm. Terrestrial CDR approaches, such as enhanced rock weathering (ERW) and biomass with carbon removal and storage (BiCRS) fit well into agricultural operations. ERW minerals, such as olivine and basalt, can be spread by agricultural workers using existing equipment. ERW minerals can also benefit crop farmers by improving soil health and boosting crop yields. Crop residues which would otherwise be disposed of can be collected and transformed into various carbon-rich materials for permanent carbon sequestration via BiCRS. Repurposing this crop residue for BiCRS also provides an additional revenue stream for crop farmers.
In this scene, spreaders typically used for distributing fertilizer are instead spraying olivine and basalt onto crop soils for ERW. This olivine and basalt have been locally sourced from the nearby quarry (see Scene 2), as indicated by the truck carrying earthy olivine at the front of the scene. Corn stover leftover after harvest is being baled and transported to be used for other terrestrial CDR projects.
Across the road from the crop farm, some of the baled corn stover is being broken up and put through a mobile biomass processing machine to turn the crop residue into bio-oil using heat via pyrolysis. Bio-oil is a viscous, carbon-rich liquid that can be injected into the ground for permanent carbon sequestration as a form of BiCRS. The bio-oil produced using this corn stover is being transported via green tanker trucks to a separate injection site (see Scene 4). A bale bed truck can be seen transporting bales of corn stover to be used for another BiCRS project down the road (see Scene 5). In the distance, a dairy farm is involved in another BiCRS project (see Scene 5).

Job Descriptions
- Custom Harvesters: Collect, organize, and transport the corn stover to be used for BiCRS projects.
- Agricultural Equipment Operators: Operate and maintain the various machinery involved in baling the corn stover for BiCRS.
- Carbon Monitoring Inspectors: Collect samples of soil and bio-oil for monitoring, reporting, and verification (MRV). Trained professionals, such agronomists or biochemists, incorporate the data collected into highly sophisticated models to ensure that the CO2 is effectively being sequestered in the soil or the bio-oil produced.
- Agricultural Equipment Operators: Operate and maintain the various machinery involved in spreading olivine and basalt for ERW.
- Agriculture Extension Agents: Educate crop farmers on how ERW works and best practices to maximize carbon sequestration and soil enhancement.
- Pyrolysis Operators: Operate and maintain the mobile biomass processing facilities that transform corn stover into bio-oil via pyrolysis.
- Operations Management and Supervision: Oversee the general operations of the mobile biomass processing facility to ensure safety and efficiency.
- Vehicle Operators: Operate a variety of vehicles, such as dump trucks transporting olivine and basalt dust to the crop farm, bale bed trucks moving corn stover to BiCRS projects, and tanker trucks carrying bio-oil to the injection site.
4. Terrestrial Carbon Removal and Subsurface Injection (Part 1)
Scene Description
Away from the crop farm, we see how terrestrial CDR technologies can be integrated into and around retired oil and gas fields. Oil and gas infrastructure and workforces translate well to terrestrial CDR methods that involve injecting materials underground. Both these sectors require skillsets related to geological surveying, drilling, pipeline transport, subsurface injection, etc. The thinking is that the same expertise and skills involved in extracting carbon from the ground can be repurposed for putting it back into the ground.
In this scene, a monitoring well and its protective ‘fort’ are being constructed alongside a completed injection fort. This injection fort is injecting a mix of CO2 and brine deep underground into ultramafic rock formations. In these formations, the CO2 mineralizes and is permanently sequestered in a process called in-situ mineralization. These forts are part of an array of injection forts connected to a solar-powered, commercial-scale direct air capture (DAC) project via CO2 pipelines. Typically, these pipelines would be underground. However, for the purpose of being able to see the pipelines in our rendering, we illustrate these pipelines to be above ground.
Further back, a former oil and gas well, as indicated by the decommissioned derrick tower, has been repurposed for injecting the bio-oil produced from corn stover as a form of biomass with carbon removal and storage (BiCRS) (see Scene 3). Once the bio-oil is injected into the sedimentary rock, it sinks and solidifies for permanent sequestration. Green tanker trucks bring bio-oil produced at various crop farms to be injected into the ground.

Job Descriptions
- Carbon Monitoring Inspectors: Analyze data output from CO2 and bio-oil injection equipment for monitoring, reporting, and verification (MRV). Trained professionals, such as geologists and biochemists, incorporate the data collected into highly sophisticated models to ensure that the CO2 is effectively being sequestered via bio-oil injection or in-situ mineralization.
- Construction Workers: Build the infrastructure for the monitoring forts. Includes welders, pipefitters, plumbers, electricians, etc.
- Engineers: Work alongside construction to install the more technical components involved in safely monitoring the CO2 injection well. Includes mechanical, industrial, chemical, civil, and electrical engineers.
- Mechanical, Electrical, and Plumbing (MEP) Maintenance: Maintain the various heating, ventilation, and air conditioning (HVAC), electrical, and plumbing systems integrated into the in-situ mineralization and bio-oil injection facilities.
- Wellhead Operators: Operate and maintain the engines, pumps, hoses, etc. involved in piping CO2 and bio-oil into the subsurface for permanent carbon sequestration.
- Service Unit Operators: Maintain CO2 and bio-oil flow through pipelines and perform safety and maintenance inspections on pipeline equipment.
- Process Engineers: Perform engineering and operation activities to ensure that the CO2 and bio-oil are being transported, injected, and sequestered safely and efficiently.
- Floorhands: Move, maintain, and repair equipment around the bio-oil injection facility so that others can do their jobs safely and efficiently. They also assist other workers with a wide range of operations and maintenance tasks on the facility floor.
- Operations Management and Supervision: Oversee the general operations of the in-situ mineralization and bio-oil injection facilities to ensure safety and efficiency.
- Vehicle Operators: Operate a variety of vehicles, such as tanker trucks transporting bio-oil to the injection site.
- Health, Safety, and Environment (HSE) Officers: Minimize hazards, prevent accidents and injuries, and promote environmentally safe and sustainable practices to protect the health and safety of workers on the construction site and the bio-oil injection facility.
5. Terrestrial Carbon Removal and Subsurface Injection (Part 2)
Scene Description
Up the road, we see more examples of how terrestrial CDR technologies can be integrated into retired oil and gas fields and farmlands. As mentioned earlier, the existing workforces, equipment, and infrastructure in the agriculture and oil and gas sectors translate well to a wide array of biomass with carbon removal and storage (BiCRS) projects. This scene highlights how cross-sectoral collaboration between legacy industries is not only vital for commercial-scale BiCRS but also potentially lucrative for these existing industries.
Here, a retired oil and gas well has been converted into a BiCRS facility that turns corn stover from nearby crop farms (see Scene 3) into CO2 and hydrogen. Once transported to the facility, the corn stover bales are broken up and organized into rows before being fed into the tall structure in the foreground which houses the gasification system. After gasification, the corn stover is now a mixture of carbon-rich syngas and biochar ash. From here, this syngas undergoes several gas processing steps and is separated into CO2 and hydrogen.
The CO2 is transported to a nearby retired oil and gas well and injected underground for permanent carbon sequestration. The hydrogen is stored on-site before being transported by tanker trucks to be used as feedstock or energy for other projects. The biochar ash is also transported to nearby crop farms to be used as a soil amendment.
Further back, we see another oil and gas well turned BiCRS project next to a dairy farm. At the dairy farm, cow manure is being collected and piped into tanker trucks to be taken to the nearby BiCRS project. At the injection site, the manure is processed, mixed with brine, and turned into a slurry waste. This slurry waste is then injected into the retired oil and gas well for permanent carbon sequestration.

Job Descriptions
- Cattle Farmers: Raise the cattle and collect manure using scoopers and loaders to produce the waste slurry that is injected at the nearby BiCRS facility.
- Carbon Monitoring Inspectors: Collect samples of waste slurry and analyze data output from CO2 and waste slurry injection equipment for monitoring, reporting, and verification (MRV). Trained professionals, such as geologists or biochemists, incorporate the data collected into highly sophisticated models to ensure that the CO2 is effectively being sequestered via CO2 or waste slurry injection.
- Mechanical, Electrical, and Plumbing (MEP) Maintenance: Maintain the various heating, ventilation, and air conditioning (HVAC), electrical, and plumbing systems integrated into all the BiCRS facilities.
- Wellhead Operators: Operate and maintain the engines, pumps, hoses, etc. involved in piping CO2 and waste slurry into the subsurface for permanent carbon sequestration.
- Service Unit Operators: Maintain CO2 and waste slurry flow through pipelines and perform safety and maintenance inspections on pipeline equipment.
- Computer-Controlled Tool Operators: Operate the computer systems controlling the technical machinery of the BiCRS facilities, i.e., waste slurry processing, the gasification system, syngas processing, etc.
- Process Engineers: Perform engineering and operation activities to ensure that the CO2, hydrogen, and waste slurry are being transported and sequestered/stored safely and efficiently.
- Floorhands: Move, maintain, and repair equipment around the BiCRS facilities so that others can do their jobs safely and efficiently. They also assist other workers with a wide range of operations and maintenance tasks on the facility floor.
- Operations Management and Supervision: Oversee the general operations of the BiCRS facilities to ensure safety and efficiency.
- Vehicle Operators: Operate a variety of vehicles, such as bale bed trucks carrying corn stover and tanker trucks carrying hydrogen and waste slurry between BiCRS projects.
- Health, Safety, and Environment (HSE) Officers: Minimize hazards, prevent accidents and injuries, and promote environmentally safe and sustainable practices to protect the health and safety of the BiCRS facility workers.
Subscribe
Get updates whenever new content is added. We'll never share your email with anyone.